K
Kirsten Korosec
Guest
General Motors has spent the past year securing a domestic supply chain for the millions of electric vehicles it plans to produce by the end of the decade, everything from battery cell manufacturing and cathode active materials to lithium and even recycling that will turn scrap into raw materials.
Now it’s locking in a domestic source of rare earth minerals, alloy and finished magnets for the electric motors it will use in its upcoming barrage of EVs including the GMC Hummer EC, Cadillac Lyriq and Chevrolet Silverado EV through a partnership with MP Materials and another separate deal with Vacuumschmelze (VAC) of Germany. The upshot: two new facilities will be built in the United States, bolstering the domestic production of rare earth magnets.
And GM will need a lot of magnets, which are a key component of electric motors that helps create the torque that propels a vehicle’s wheels. The automaker plans to bring 30 new EVs to the global market by 2025 and to transition to an all zero-emission portfolio by 2035. The GMC Hummer alone may have many as three motors with up to 11,500 pound-feet of torque.
Under the partnership with VAC, GM and the German company will build a plant in the U.S. that will manufacture permanent magnets for the electric motors. The agreement with VAC is non-binding at the moment. GM executives said in a briefing call Thursday that the two companies are expected to finalize definitive agreements in early 2022. The plant is expected to start production in 2024. The location of the facility will be announced at a later date, the companies said.
The agreement with MP Materials is more of a mines-to-magnets partnership. Rare earth materials will be mined and processed at MP Materials’ mine in California, then transformed into metal and magnets in a new 200,000-square-foot facility in Fort Worth, Texas. Recycling will be integrated at both locations, according to MP.
The facility, pictured in a rendering below, will produce NdFeB alloy and magnets with the potential to power about 500,000 EV motors per year, the companies said. A gradual production ramp is expected to begin in 2023.

Image Credits: MP Materials
The deal is a notable one for MP Materials, which owns and operates the only active and scaled rare earth production site in the United States. The Mountain Pass site, once the world’s largest producer of rare earths, has moved through a few hands over the past several decades. Chevron sold it to a company called Molycorp in 2008. The company intended to restart and even expand the mine but eventually was forced into bankruptcy.
MP Materials acquired Mountain Pass in July 2017. The site wasn’t operational, according to MP and just eight employees were left to care and maintain it. MP has since restarted operations and by 2020 the Mountain Pass site, pictured below, produced more than 38,500 metric tons of rare earth contained in concentrate, representing more than 15% of global production according to the U.S. Geological Survey.
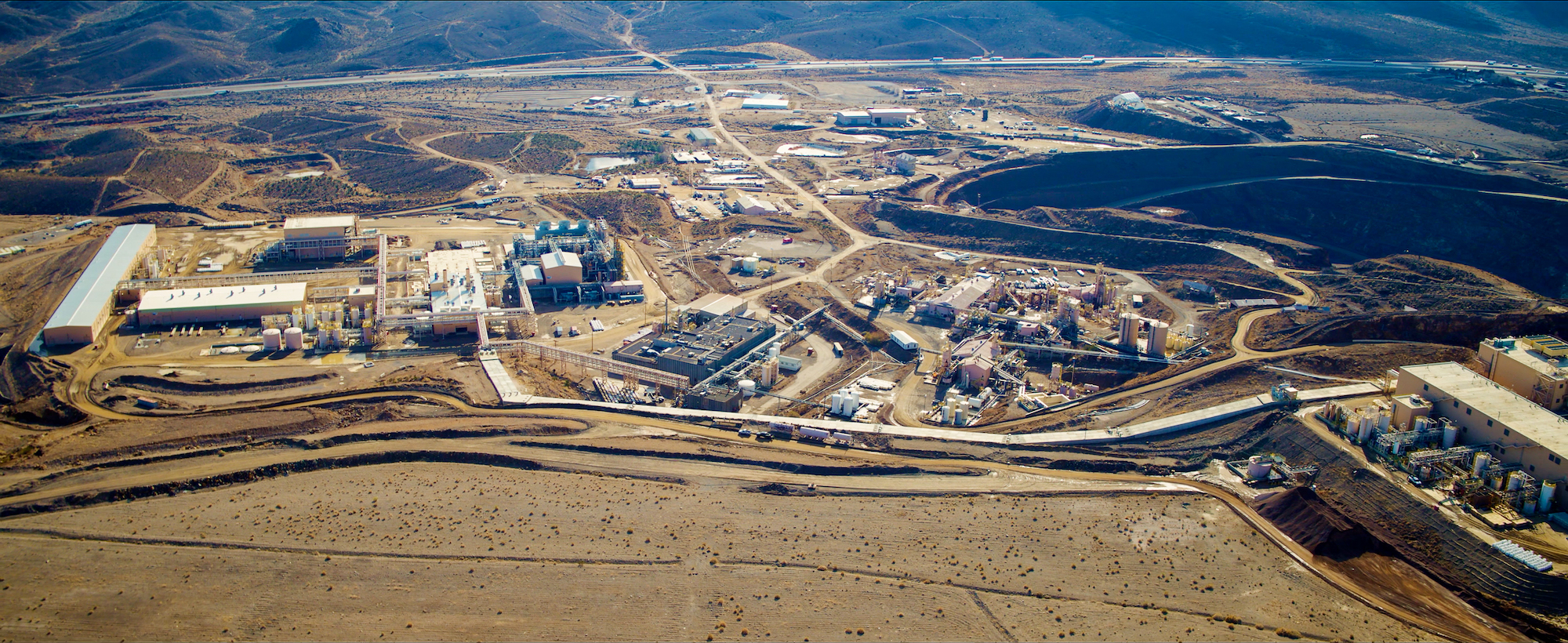
Image Credits: MP Materials
It’s also a milestone for advocates of U.S.-based rare earth production. Rare earth materials can be found all over the world and were once mined in the United States. But companies stopped mining rare earths by 2003, opting instead to buy them from China. Today, nearly all of the mining is in China .The development of Neodymium-iron-boron (or NdFeB) permanent magnets — which are used in electric motors — began in the United States, but today the main producers are in China, Brazil and India. China has about 90% of the sintered rare earth magnet capacity.
The Fort Worth facility will be be used to supply NdFeB alloy flake to other magnet producers to help develop a diverse and resilient U.S. magnet supply chain, GM and MP Materials said in their joint announcement. MP Materials said the Fort Worth facility will consume less than 10% of the 6,075 tonnes of NdPr oxide it expects to produce annually at Mountain Pass.
GM announced in October another non-binding agreement with General Electric’s clean energy arm GE Renewables to collaborate on the supply of rare earth materials and to look for ways to improve supplies of magnets, copper and electrical steel. The two companies announced intentions at the time to also explore new supply chains for copper and “eSteel,” a material composed in part of recycled materials, to be used in automotive traction motors and renewable power generation.
That deal still appears to be moving forward. A GM spokesperson said in an email that “collaboration is an important component of building a strong, resilient and scalable North America-focused EV supply chain. We are still in the process of finalizing definitive agreements.”
Now it’s locking in a domestic source of rare earth minerals, alloy and finished magnets for the electric motors it will use in its upcoming barrage of EVs including the GMC Hummer EC, Cadillac Lyriq and Chevrolet Silverado EV through a partnership with MP Materials and another separate deal with Vacuumschmelze (VAC) of Germany. The upshot: two new facilities will be built in the United States, bolstering the domestic production of rare earth magnets.
And GM will need a lot of magnets, which are a key component of electric motors that helps create the torque that propels a vehicle’s wheels. The automaker plans to bring 30 new EVs to the global market by 2025 and to transition to an all zero-emission portfolio by 2035. The GMC Hummer alone may have many as three motors with up to 11,500 pound-feet of torque.
Under the partnership with VAC, GM and the German company will build a plant in the U.S. that will manufacture permanent magnets for the electric motors. The agreement with VAC is non-binding at the moment. GM executives said in a briefing call Thursday that the two companies are expected to finalize definitive agreements in early 2022. The plant is expected to start production in 2024. The location of the facility will be announced at a later date, the companies said.
The agreement with MP Materials is more of a mines-to-magnets partnership. Rare earth materials will be mined and processed at MP Materials’ mine in California, then transformed into metal and magnets in a new 200,000-square-foot facility in Fort Worth, Texas. Recycling will be integrated at both locations, according to MP.
The facility, pictured in a rendering below, will produce NdFeB alloy and magnets with the potential to power about 500,000 EV motors per year, the companies said. A gradual production ramp is expected to begin in 2023.

Image Credits: MP Materials
The deal is a notable one for MP Materials, which owns and operates the only active and scaled rare earth production site in the United States. The Mountain Pass site, once the world’s largest producer of rare earths, has moved through a few hands over the past several decades. Chevron sold it to a company called Molycorp in 2008. The company intended to restart and even expand the mine but eventually was forced into bankruptcy.
MP Materials acquired Mountain Pass in July 2017. The site wasn’t operational, according to MP and just eight employees were left to care and maintain it. MP has since restarted operations and by 2020 the Mountain Pass site, pictured below, produced more than 38,500 metric tons of rare earth contained in concentrate, representing more than 15% of global production according to the U.S. Geological Survey.
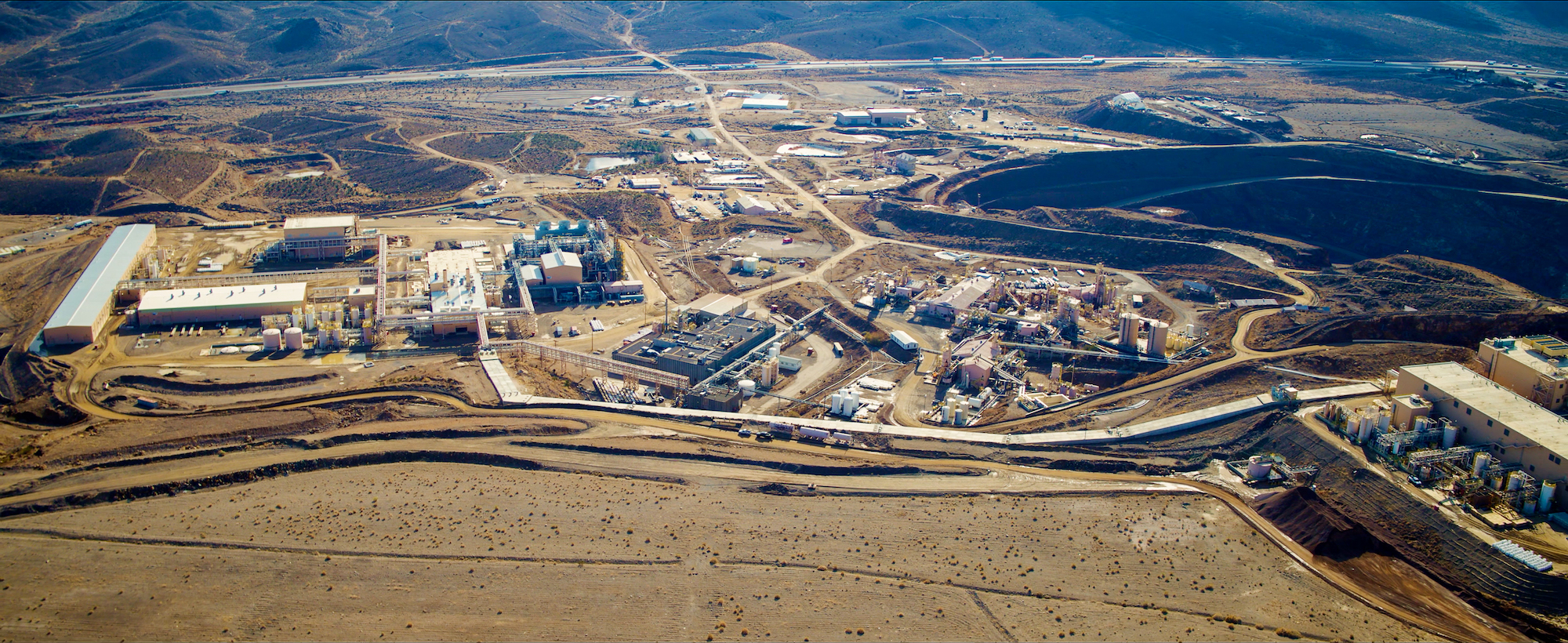
Image Credits: MP Materials
It’s also a milestone for advocates of U.S.-based rare earth production. Rare earth materials can be found all over the world and were once mined in the United States. But companies stopped mining rare earths by 2003, opting instead to buy them from China. Today, nearly all of the mining is in China .The development of Neodymium-iron-boron (or NdFeB) permanent magnets — which are used in electric motors — began in the United States, but today the main producers are in China, Brazil and India. China has about 90% of the sintered rare earth magnet capacity.
The Fort Worth facility will be be used to supply NdFeB alloy flake to other magnet producers to help develop a diverse and resilient U.S. magnet supply chain, GM and MP Materials said in their joint announcement. MP Materials said the Fort Worth facility will consume less than 10% of the 6,075 tonnes of NdPr oxide it expects to produce annually at Mountain Pass.
GM announced in October another non-binding agreement with General Electric’s clean energy arm GE Renewables to collaborate on the supply of rare earth materials and to look for ways to improve supplies of magnets, copper and electrical steel. The two companies announced intentions at the time to also explore new supply chains for copper and “eSteel,” a material composed in part of recycled materials, to be used in automotive traction motors and renewable power generation.
That deal still appears to be moving forward. A GM spokesperson said in an email that “collaboration is an important component of building a strong, resilient and scalable North America-focused EV supply chain. We are still in the process of finalizing definitive agreements.”